
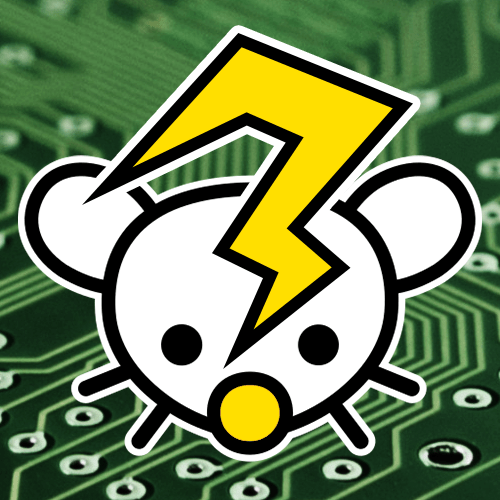
I suggest that you give details of the iron (and tip) and solder that you are using and a close up photo of the wires that are being problematic.
The iron temperature control may be faulty and the iron just not getting to soldering temperatures. Or you may have it set too low.
The thermal mass of typical USB wires is so low that, if the solder actually melts freely at the tip end when not soldering anything, it should do so when soldering these wires.
On a KISS basis - I tend to just use a bimetallic switch or omit the temperature control and just run the fan from power up. It’s possible for a processor to suffer some non-handled exception where it no longer executes the temperature management routine.